Material Property Quick Reference Chart (Relation between WC average grain diameter and hardness)
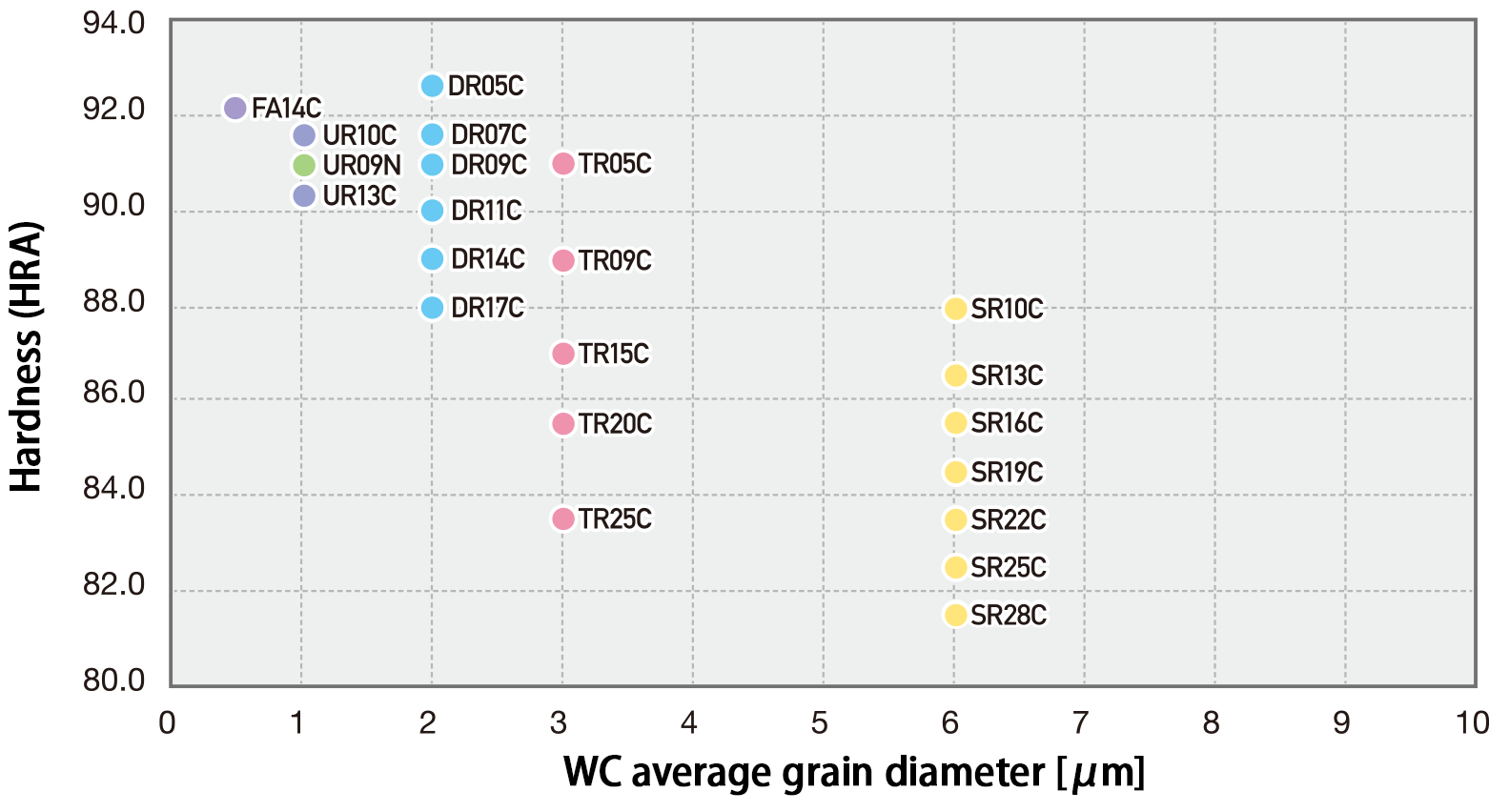
Main Material Property Table*1
Material property | JIS classification*2 | Material name*3 | Hardness | Specific gravity | Deflective strength GPa |
Fracture toughness MPa・m1/2 *5 |
Compression strength GPa |
High pressure HIP availability | |
---|---|---|---|---|---|---|---|---|---|
HRA | Hv | ||||||||
Ultrafine particles / High abrasion resistance | VF-20 | FA14C | 92.0 | 1700 | 13.9 | 4.1※4 | 12 | 5.5※4 | ○ |
Fine particles Abrasion resistance |
VF-30 | UR10C | 91.5 | 1630 | 14.5 | 4.0 | 13 | 5.3 | ― |
VF-40 | UR13C | 90.5 | 1500 | 14.2 | 4.1 | 16 | 4.8 | ― | |
耐食性 耐摩耗 |
VM-20 | DR05C | 92.5 | 1800 | 15.0 | 3.9※4 | 11 | 5.5※4 | ○ |
VM-30 | DR07C | 91.5 | 1630 | 14.8 | 3.6 | 13 | 5.5 | ― | |
VM-30 | DR09C | 91.0 | 1560 | 14.6 | 3.7 | 14 | 5.3 | ― | |
VM-40 | DR11C | 90.0 | 1450 | 14.4 | 3.8 | 17 | 5.2 | ― | |
VM-40 | DR14C | 89.0 | 1350 | 14.1 | 3.9 | 20 | 4.8 | ― | |
VM-50 | DR17C | 88.0 | 1210 | 13.8 | 3.8 | 24 | 4.4 | ― | |
Corrosion resistance Abrasion resistance Impact resistance |
VC-40 | TR05C | 91.0 | 1560 | 15.0 | 3.4※4 | 14 | 4.6※4 | ○ |
VC-40 | TR09C | 89.0 | 1350 | 14.6 | 3.3 | 20 | 4.4 | ― | |
VC-50 | TR15C | 87.0 | 1100 | 14.0 | 3.2 | 29 | 4.0 | ― | |
VC-60 | TR20C | 85.5 | 940 | 13.5 | 3.1 | 38 | 3.7 | ― | |
VC-70 | TR25C | 83.5 | 800 | 13.0 | 3.0 | 55 | 3.3 | ― | |
Corrosion resistance Impact resistance |
VU-50 | SR10C | 88.0 | 1210 | 14.5 | 3.0 | 24 | 4.0 | ― |
VU-60 | SR13C | 86.5 | 1050 | 14.2 | 2.9 | 32 | 3.8 | ― | |
VU-60 | SR16C | 85.5 | 940 | 13.9 | 2.8 | 38 | 3.6 | ― | |
VU-70 | SR19C | 84.5 | 860 | 13.6 | 2.7 | 46 | 3.4 | ― | |
VU-70 | SR22C | 83.5 | 800 | 13.3 | 2.6 | 55 | 3.2 | ― | |
VU-70 | SR25C | 82.5 | 750 | 13.0 | 2.5 | (66) | 3.0 | ― | |
VU-80 | SR28C | 81.5 | 710 | 12.7 | 2.4 | (80) | 2.9 | ― | |
High corrosion resistance / Anti-ferromagnetism | NF-30 | UR09N | 91.0 | 1560 | 14.5 | 4.0※4 | 14 | 4.9※4 | ○ |
Material property | JIS classification*2 | Material name*3 | HRA | Hv | Specific gravity | Deflective strength GPa |
Fracture toughness MPa・m1/2 *5 |
Compression strength GPa |
High pressure HIP availability |
Hardness |
- Main material property table: Shows representative values, not guaranteed values.
- JIS classification: This complies with the JIS B4054:2020 cemented carbide alloy standard for abrasion resistant tools.
- Material name: Refer to "Material Name Code"
- Deflective strength (compression strength): Values after application of high pressure HIP
- Fracture Toughness: Vickers Indentation Method. Calculated from the recommended formula of TAS 0059:2023.Values in parentheses are reference range.
Material name code key:

1st digit
WC average grain diameter (μm) | Code |
0.5≧ | F |
0.8~1.2 | U |
1.5~2.0 | D |
2.5~3.5 | T |
5.0~7.0 | S |
2nd digit
Additive | Code |
None | - |
Additive ① | R |
Additive ② | A |
3rd and 4th digits
Indicates bonded phase amount |
末尾
Last digit | Code |
Co | C |
Ni | N |
Material Type
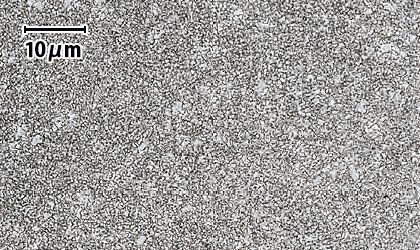
① FA-C type (High abrasion resistance ultrafine particle alloy)
This alloy uses ultra-fine WC particles and is superior in abrasion resistance to the UR-C type. It is used for sliding parts and light-load press parts where hardness and abrasion resistance are important.
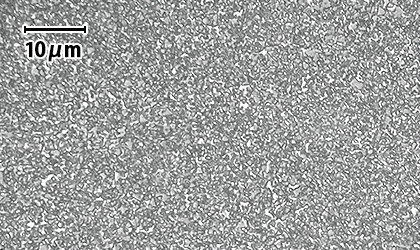
② UR-C type (High abrasion resistance fine particle alloy)
This alloy uses fine WC particles and is superior in abrasion resistance to DR-C. It is used for slitter knives and punches for electronic components due to its excellent mirror finish and edge sharpness.
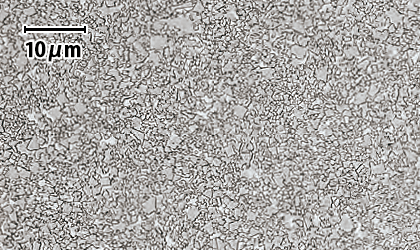
③ DR-C type (Abrasion resistant material)
This alloy is made of fine WC particles and features abrasion resistance. It also has excellent corrosion resistance and is used in a wide range of fields.
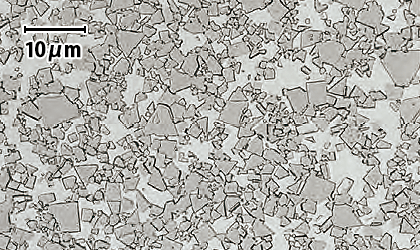
④ TR-C type (Abrasion and impact resistant material)
This alloy is made of medium-grain WC particles and features a good balance between impact resistance and abrasion resistance.
It also has excellent corrosion resistance, and is highly regarded in the field of cold forging dies, with a great track record.
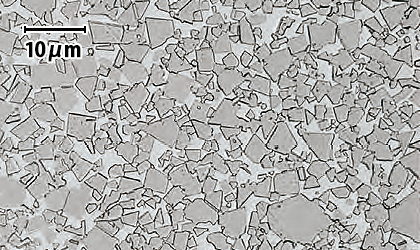
⑤ SR-C type (Impact resistant material)
This alloy is made of coarse WC particles, and features outstanding impact resistance as well as corrosion resistance.
It has superior toughness compared to TR-C alloys and has a great track record in the extreme cold forging die and warm forging fields.
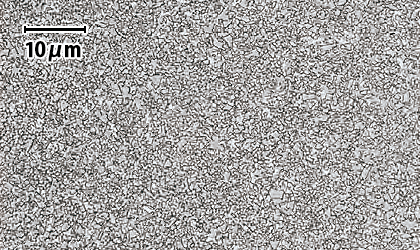
⑥ UR-N type (High corrosion resistance / Anti-ferromagnetism)
This alloy has excellent corrosion resistance compared to other materials, due to its Ni binding. It is non-magnetic under normal environmental conditions.
Due to these characteristics, it has been used in food and pharmaceutical industries, high-pressure pump parts, magnetic field molds, canning dies, etc., receiving high evaluation.
Precautions
1 Precautions for handling cemented carbide products
- Since cemented carbide may be broken by impact such as dropping, etc., please make sure that there are no chips, cracks or other abnormalities in the product.
- The apparent density of cemented carbide is more than 1.5 times that of steel materials. Take care to avoid dropping it on your hands or feet when handling.
- Depending on the product shape (thin products, products with notches, etc.), small impacts or load stresses may cause cracking. Therefore, when fixing the product to a machine or other equipment during processing or use, please consider the method and take extra care.
- Since cemented carbides are vulnerable to impact, chipping or cracking may occur when coming into contact with each other or with other metals.
2 Precautions when processing cemented carbide
❶Grinding and polishing
- Cemented carbide may crack or split when subjected to excessive machining stress. During machining, make sure that the workpiece is firmly secured to the bed, chuck, or other fixed part.
- Never use a metal hammer or similar object to directly strike the product, as this may cause cracking or chipping.
- Cemented carbide does not easily adhere to magnets; make sure it is firmly in place when using magnets to secure it.
- Ground or polished cemented carbides are slippery and their corners are sharp; please handle machined products with care.
❷Electrical discharge machining (Diemilling EDM and wire EDM)
- The strength of cemented carbide decreases when electrical discharge machining is performed, thus cracks and other damage can easily occur. Please configure the machining conditions and method in consideration of the intended use.
- Cemented carbide may crack during wire EDM; please make sure that there are no cracks after wire processing, and perform post-processing.
❸Brazing
- Cemented carbides may crack during brazing. Confirm that there are no cracks before and after brazing.
- The surface of cemented carbide may be oxidized via heating in air; please remove the oxidized part after brazing.
❹Cautions for general operation
- In rare cases, some people may be allergic to cemented carbide; please wear gloves or other protective gear. Dust may also affect the human body; please wear a dust mask.
- Cemented carbide may become damaged during machining; be sure to use safety devices and safety covers, etc. on the machine and elsewhere. Also, the operator should wear safety glasses, safety shoes, etc.
- Cemented carbides contain metals of the iron group (cobalt and nickel).
Please handle with care as corrosion (rust) will occur if exposed to an oxidizing atmosphere.
3 Precautions for disposal
- Although they do not contain any RoHS2 substances or other hazardous materials, please consult with a specialist or our company regarding the disposal of cemented carbides, as they may affect the natural environment.